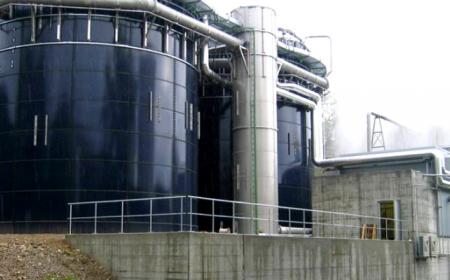
Biological treatment removes dissolved organic hydrocarbons from water. Flootech’s sophisticated, compact Floobed® Moving Bed Biofilm Reactor (MBBR) uses special, freely moving biofilm carriers, which suit high capacity operations, are particularly tolerant of variations in feed flow rate and quality, and give consistently high quality results.
Most of the microbes cultivated for purification grow attached as a film on the surface of the Floobed® MBBR’s carrier elements. Our design avoids the blocking problems that are a traditional hazard of attached microbiological growth processes. A specially designed bottom aeration system mixes the carrier elements amongst the treated water efficiently. The biomass that remains when water flows out of the bioreactor is separated by secondary clarification or micro flotation.
Having a limited footprint and high specific efficiency, our Floobed® MBBR carrier can be introduced to existing active sludge processes to meet higher capacity or more stringent quality requirements when required.
The FlooBed® MBBR process can be built to have one or several stages in series or in parallel. Excess sludge is removed from the carriers continuously by intensive mixing and abrasion. Microflotation is typically used for subsequent separation, or sedimentation, if applicable. Part of the sludge is recycled back to the FlooBed® system, and the rest is further dewatered.
Advantages of the FlooBed® MBBR:
- A FlooBed® carrier is easy to operate because it is very tolerant to peaks of organic load and variations in flow rate. It tolerates temperature variations and toxins in the feed water.
- The reactor volume needed for a FlooBed® system is considerably smaller compared to activated sludge plants. Space requirement is typically 10-40% of conventional solutions.
- The FlooBed® carrier has an open structure, which facilitates a high amount of biomass and improves mass transfer efficiency. The durable structure of the carriers makes them tolerant to mechanical abrasion, resulting in low maintenance costs.
The filling ratio of carriers can be adjusted on a case by- case basis. In practice, this means the process is designed to be very flexible. Filling can be changed according to flow and load, and the FlooBed® carrier can be also built into an existing basin.
In fixed-film reactors, clogging caused by excess sludge can be a problem. The FlooBed® system minimizes this by creating turbulence that churns the water through the carriers, thus no backwashing is needed.
Design Parameters:
- Retention time typically from 1 to 4 hours.
- Organic load range 2–20 kg BOD/m3d.
- Biomass concentration in the reactor 6-12 kg/m3.
- On average 70–80% of microbes attach on the carriers.
- Low sludge circulation, 0–15% of the in-feed flow.
- Efficient aeration.
- Wide range of operating temperatures.
- Carrier filling ratio 20–60% of biomass and improves mass transfer efficiency.
The FlooBed® solution has been selected for several applications, such as effluents from process industries, landfill leachate and municipal wastewaters. In the pulp and paper industry, FlooBed® has been built into the mill area for pretreatment of existing activated sludge plants and for new mills with high requirements.
Anaerobic Biological Treatment
Reduce carbon and water footprint, recover energy and improve operational sustainability.
Anaerobic treatment systems are based on a biological process operated and controlled under anaerobic conditions that effectively treat COD, BOD, and VSS while producing biogas and very little biomass (without oxygen). Econvert is within the Nijhuis Saur Industries group, the company and brand name of our Anaerobic solutions with vast experience and know-how to properly select, design, build and operate anaerobic processes, providing clients with the best treatment solution. In general, aerobic and anaerobic treatment solutions are both methods using bacteria and can be used together for the effective removal of contaminants meet CSR goals, and meet environmental compliance.
Why apply anaerobic solutions?
- High return on investment
- Up to 90% savings on discharge costs
- Low operational costs and low maintenance
- Conversion of wastewater into renewable energy
- No sludge discharge costs
- Reduction of CO2 footprint
- Good possibilities for water reuse in factories (towards closed loops)
- Quick start-up
- Economically appealing at COD loads starting from 300 kg per day
Depending on the application, anaerobic solutions can be applied to several types of industrial wastewater. Food, Beverage, Dairy, Municipal and Heavy Industries contain several contaminants which are suitable to remove COD and generate electricity from the wastewater.
Founded on in-depth process knowledge, Nijhuis Saur Industries and Econvert offers customized solutions. We design and construct the following water and biogas treatment plants.
- Econvert-UASB® (Upflow Anaerobic Sludge Blanket)
Robust configuration enables the handling of large varieties in both volume and composition - Econvert-EGSB® (Expended Granular Sludge Bed)
The optimized compromise, combining a small footprint with less internals. The unique settling system of the reactor has proven to retain solids also in high flow. - Econvert-IR® (Internal Recirculation)
A high performer technology and designed to create the ideal process conditions. The two-stage settling system enables internal recirculation - Econvert-Dsulph® (biological biogas desulphurization)